Nous avons tous vu leur travail, mais peu d'entre nous réalisent que les costumes de James Bond depuis l'époque de Pierce Brosnan ; la tenue de cérémonie de l'équipe britannique aux derniers Jeux olympiques et de l'équipe de football d'Angleterre lors des deux dernières Coupes du monde ; les célèbres vestes vertes du Masters de golf à Augusta ; de nombreux vêtements vendus dans les boutiques élégantes de marques telles que Burberry, Paul Smith, Chanel, Tom Ford, Hermès et Gucci sont tous passés par une combinaison de traitements sophistiqués, affinés, peaufinés et perfectionnés à travers les âges de l'usine de finissage textile W.T. Johnson : une entreprise familiale d'Huddersfield fondée en 1910 qui prend la perfection très au sérieux.
« Notre travail consiste à sublimer le tissu de nos clients : le nettoyer, en améliorer la texture, la tenue et le drapé, et le stabiliser pour que le fabricant de vêtements suivant puisse l'utiliser correctement », explique le directeur général Paul Johnson qui, avec son frère Dan, est la quatrième génération de Johnson à la tête de l'entreprise. « Si nous ne faisons pas notre part, l'utilisateur est lésé. Un tissu complètement fini fait la différence entre un costume qui durera dix ans et un autre qui ne durera que trois ans. Il est possible de faire notre travail plus rapidement pour moins cher, mais si vous êtes un client exigeant vous pourrez différencier très facilement un morceau de tissu qui a été fini rapidement à peu de frais d'un autre qui a été fait lentement et correctement. »
Les machines utilisées par W.T. Johnson pour mener à bien ses activités sont archaïques en apparence. Le premier appareil imposant que l'on découvre en visitant l'usine est un chariot à écurage enchâssé dans un tonneau géant en planches de bois qui rappelle un wagon tzigane en bois. À l'intérieur, des longueurs de tissu sont lavées dans un mélange d'eau chaude et de savon naturel, puis pressées entre des rouleaux en ekki, un bois dur africain résistant à l'eau et antidérapant que l'on utilise aussi pour les ponts, les planchers et la construction. La machine – qui fonctionne comme celles utilisées il y a plus de 100 ans – est particulièrement adaptée à l'écurage des tissus en laine les plus fins car elle effectue le travaille lentement et en douceur (chaque morceau de tissu est soumis à une séance de deux heures).
Puis vient l'étape du foulage, au cours de laquelle le tissu est feutré en l'écrasant entre deux plaques de métal dans un environnement brûlant et humide. « Cette étape rend le tissu plus chaud et plus dense et adoucit les contrastes entre les couleurs. Les créateurs imaginent donc des motifs en gardant ces effets à l'esprit », explique le directeur technique Alan Dolley qui est entré dans l'entreprise à l'âge de 16 ans, il y a 40 ans. Pour illustrer son propos, il lève un morceau de tissu dont le motif écossais a un aspect légèrement flou, comme s'il avait été réimaginé par un peintre impressionniste.
Johnson dit que la finition relève à la fois de l'art et de la science et la tâche des opérateurs, lors du foulage, en est un exemple frappant. En tenant compte de la teneur spécifique en laine prévue par les recettes (les tissus sont toujours un mélange de différents lots de laine) ainsi que des différents résultats recherchés – tels que « l'écrasé léger » et « la flanelle aveugle » –, ils doivent calculer exactement comment programmer la machine afin d'obtenir le poids, la densité et les dimensions souhaités, en prenant en compte le rétrécissement. « Nous savons exactement quelle fibre perdra en volume à la suite de différents procédés et selon certains paramètres », explique Dolley.
Certains des équipements impressionnants de W.T. Johnson ont été conçus sur place par ses propres ingénieurs, tels que les séchoirs de l'usine. Ils retrempent le tissu uniformément avant d'aspirer l'eau – on pourrait penser que c'est paradoxal, mais le morceau de tissu trempé forme un joint d'étanchéité qui rend le séchage par aspiration plus efficace.
Gallery
Plus loin, on découvre les processus chimiques qui ajoutent un facteur anti-odeur, une protection antibactérienne et une imperméabilité à l'eau semblable au Téflon, ainsi qu'une machine ressemblant à une tondeuse à gazon géante hyper sensible, qui élimine les fibres clairsemées de la surface des longueurs de tissu qui passent à travers. Puis nous arrivons devant la pièce de résistance de W.T. Johnson : une paire d'Ekofasts : des machines de décatissage en continu associant l'exposition à des températures élevées (135 degrés) et le pressage intensif en un même procédé afin d'obtenir une stabilisation et une tenue supérieure.
Il y a au moins une personnalité dans le monde de la mode qui apprécie le travail unique d'Ekofast. « Dans les années 80, lorsque Ralph Lauren se faisait un nom, il décida qu'il ne voulait pas de ce qui se vendait sur Savile Row et partout ailleurs », se rappelle Paul Johnson. « Il voulait quelque chose de luxueux, mais qui semblait aussi avoir appartenu à votre grand-père et être resté dans le grenier pendant un certain temps. Nous nous sommes associés et la finition Ralph Lauren Polo classique que nous avons créée est toujours d'actualité. »
Les deux machines devant lesquelles nous nous tenons maintenant – dont l'une a été achetée pour la somme de 300 000 £ dans les années 70 par Peter, le père de Johnson, un ingénieur devenu président de la société, et l'autre installée 10 ans plus tard – jouent un rôle essentiel pour satisfaire les exigences de M. Lauren et sont uniques au monde. « Le tissu qui en sort est qualifié de "noble" dans notre jargon », explique Dolley. « Ralph Lauren recherchait un tissu "brillant mais sans éclat" – le toucher du cachemire mais l'aspect du tweed Harris. Ils sont venus nous voir et ils ont trouvé ce qu'ils recherchaient. » Les machines ajoutent aussi un facteur de contrôle de la qualité du dressage de la trame. « Personne d'autre sur la planète n'en possède une et elles sont absolument essentielles pour un grand nombre de nos finitions », ajoute Johnson.
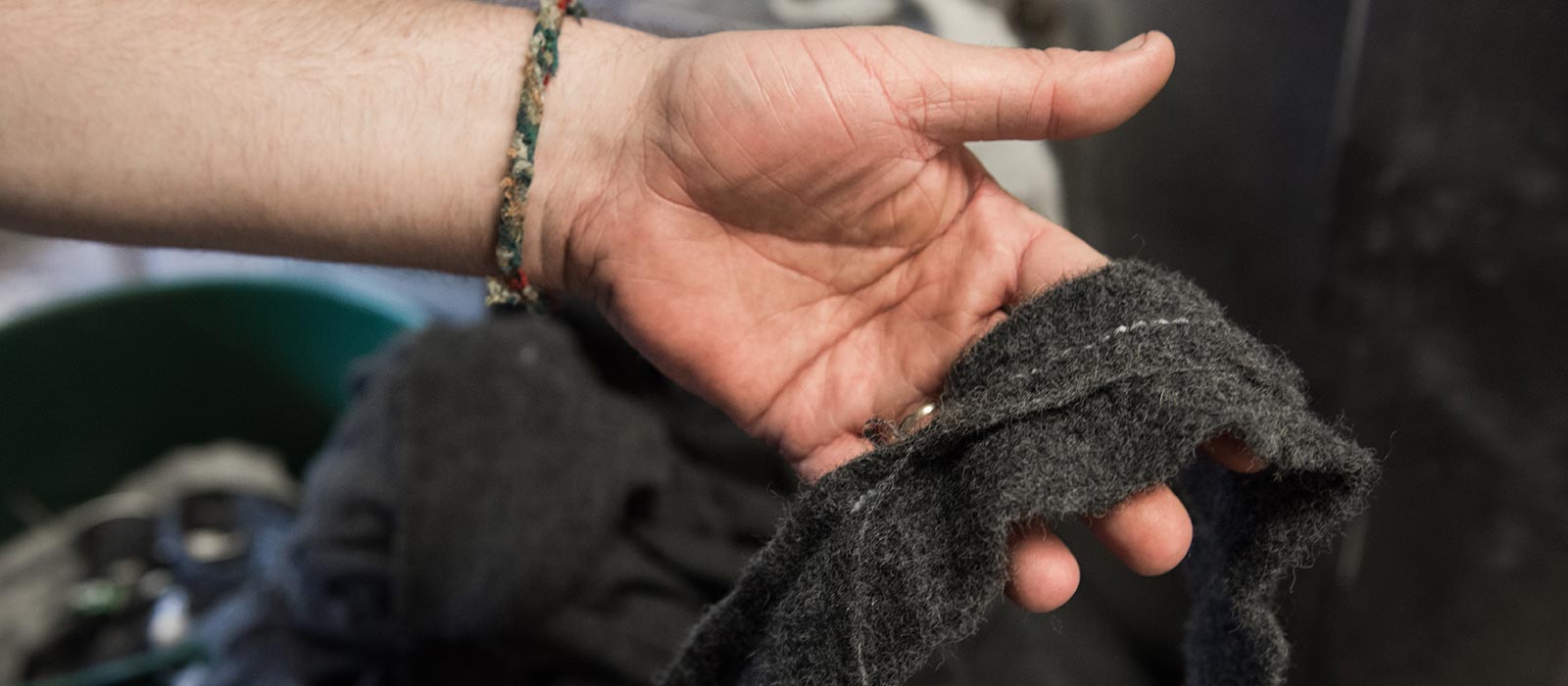
L'emplacement de l'usine est aussi important que cet équipement sophistiqué, notamment en raison de l'eau. « Un approvisionnement régulier en eau douce non contaminée est absolument primordial pour notre entreprise », affirme Johnson. « Les sociétés de distribution d'eau ne peuvent plus le garantir car elles l'acheminent d'un peu partout et ne sont pas en mesure d'en garantir l'homogénéité. » Heureusement, depuis près d'un siècle, la société puise sa propre eau grâce à un forage réalisé dans les années 1930. « La plupart des forages ont une profondeur de 300 pieds, le nôtre fait 1 500 pieds », dit-il fièrement. « La pluie tombe sur les Pennines, se fraie un chemin à travers diverses strates rocheuses et s'infiltre dans les ponceaux. Nous la recueillons et, ô surprise, elle est très homogène et très douce. »
Être au cœur de la région de production lainière traditionnelle du Yorkshire du Sud est certainement un avantage mais ce n'est pas une entreprise obsédée par le passée. Toujours soucieuse d'élargir son répertoire, W.T. Johnson assure aujourd'hui la finition d'écharpes, de châles, de plaids et de tissus d'ameublement tels que les coussins, les rideaux et les revêtements de sièges. « Nous traitons désormais du tissu pour des hôtels, des banques, des immeubles de bureau, des autocars et aussi certains tissus techniques : nous pouvons les rendre plus faciles à porter ou plus adaptés à l'usage auquel ils sont destinés. Nous offrons vraiment un service sur mesure. »
C'est une organisation fière, et à juste titre : les finisseurs sont les héros méconnus de l'industrie lainière dont les efforts pourraient être comparés à ceux des meilleurs producteurs de musique : des alchimistes anonymes travaillant sans relâche discrètement pendant que d'autres reçoivent tous les louanges. Lorsque vous aurez découvert leur travail de vos propres yeux, vous ne pourrez plus vous empêcher de saluer silencieusement leurs efforts à chaque fois que vous sortirez du garde-robe votre vêtement en laine préféré.